Manufacturing, Production and Operations
Manufacturing, Production and Operations
For effective distribution and supply chain management, businesses require the ability to automate processes and reduce errors in purchasing, order fulfillment, inventory tracking and customer support. Leading businesses turn to robust and flexible software to manage finance, operations, supply chain, distribution and more in one place to transform their operations.
How it Works
- Plan production based on customer demand and supplier cycles using capacity planning, bill of materials management and shop floor controls
- Automate data collection and reporting with business intelligence functionality to provide production managers with real-time data
- Manage relationships throughout the supply chain, from sourcing to vendor management, procurement to transportation logistics
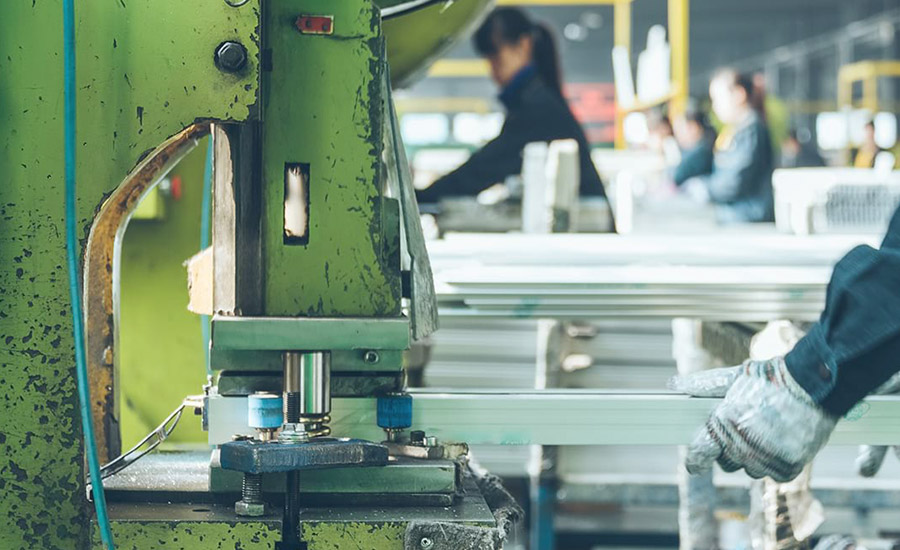
Beginner's Guide to ERP: Manufacturing
Learn which features and functionality to look for in an ERP and how to go about choosing the right solution for your manufacturing business.
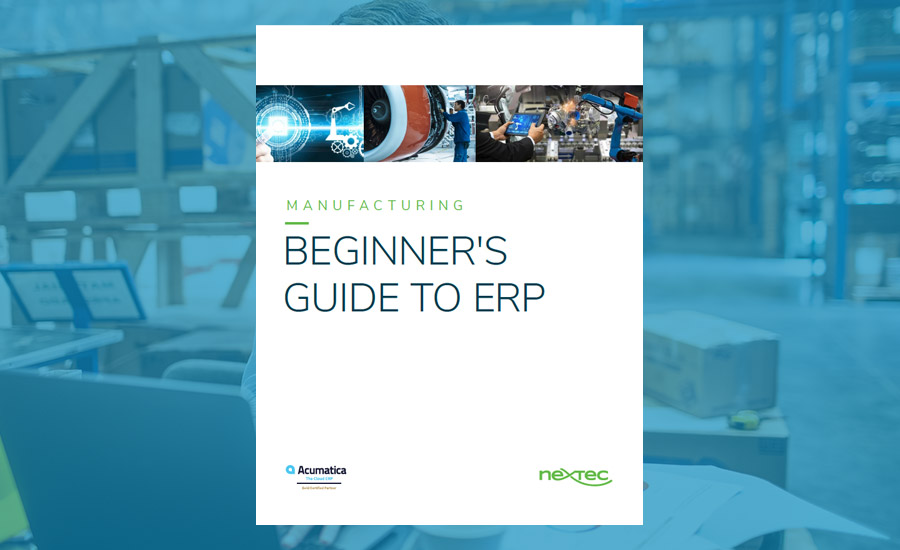
Features of Manufacturing, Production and Operations Software
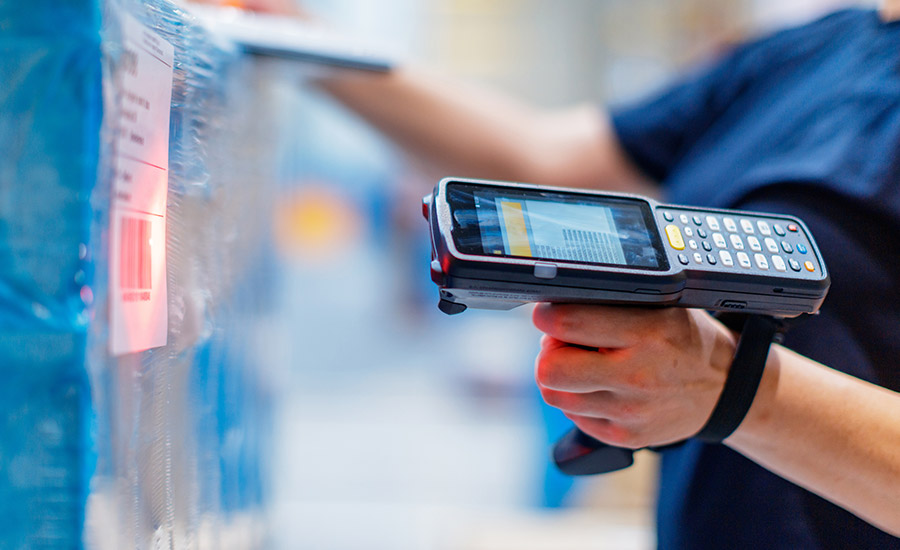
Gain Inventory Visibility
Trace every material and product with lot, sub-lot and serial number traceability functionality for a full view of inventory at all times.
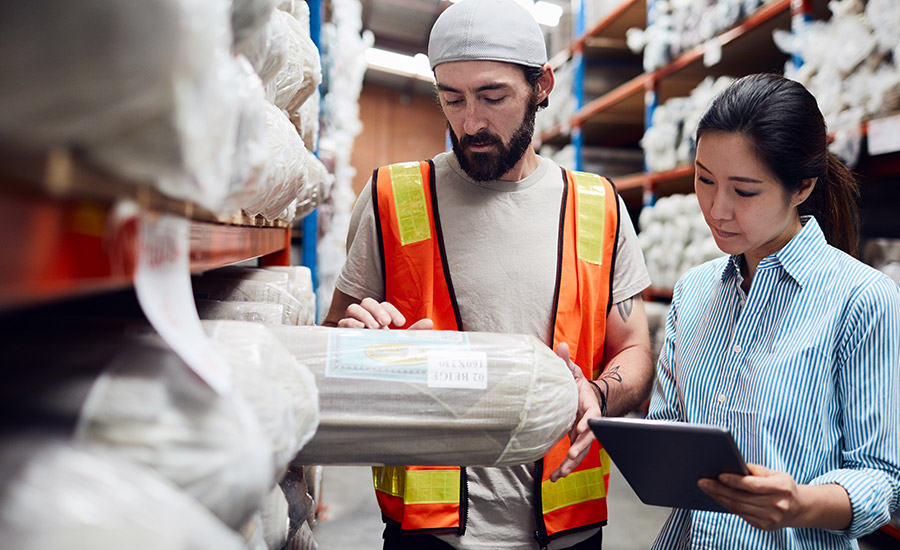
Increase Quality
Customize quality assurance criteria based on specific products and manage expiration dates, stock inspections and traceability.
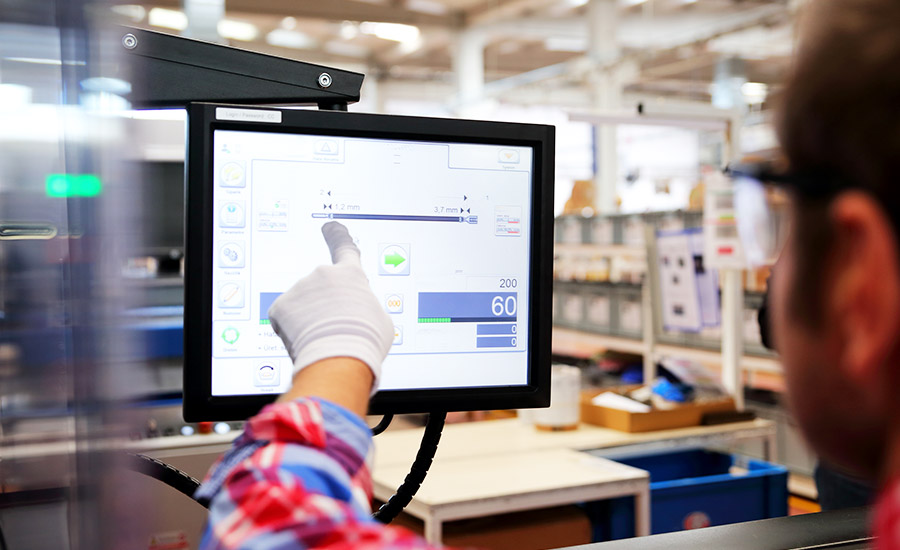
Ensure Compliance
Increase your ability to meet and report on changing regulations with automated lot traceability, detailed audit trails and access to more accurate data.
Helpful Resources
Solutions for All Your Business Needs
Growing businesses need the right tools to manage operational complexities and costly inefficiencies. Learn how NexTec can help you find a solution for your company’s unique needs.