Industry 4.0 is driving innovation and improving manufacturing business processes around the world.Digitalization is often referred to as the fourth industrial revolution, or Industry 4.0. While digital transformation has come quickly to certain industries, including consumer products, finance, and banking, manufacturing has been slower to adopt the innovations that come with digitalization.
Companies that embrace the opportunities of digital transformation and information technology have the chance to rewrite the playbook within their industry. Digital transformation opens up significant possibilities around business models, business processes, and the work itself.
Below is the modern manufacturer’s guide to digitalization.
Why digitalization matters
The rapid change taking place in varied industries points to the opportunity of digital innovation. Companies are rewriting whole business models to leverage technological opportunities. For some companies, that means entering new industries and market share. Think about the roles companies like DoorDash and Uber have played in the food service and transportation industries, respectively. Consider the impact of microlending in rural areas by new banking companies that are gaining market share in areas where markets previously did not exist.
For manufacturing companies, the old way of doing things will not suffice in a digital world. Companies need to adapt or risk being left behind as competitors or new players encroach on existing markets.
Digital technologies are ubiquitous and felt throughout the manufacturing value chain. R&D, supply chain, operations, warehousing, distribution, and transportation all have seen digital transformation change the way work is done. These technologies do not just disrupt business models; they can also transform how work is completed.
For example, information technology today allows partners throughout the supply chain to interact, using the same real-time data to pinpoint problems and solutions. Remote employees, working on multiple devices and in different time zones, can access data and interact in ways that were not feasible just a few years ago. By allowing designers, suppliers, operations managers, and distribution leaders to work together, dramatic efficiencies can be gained that reduce downtime.
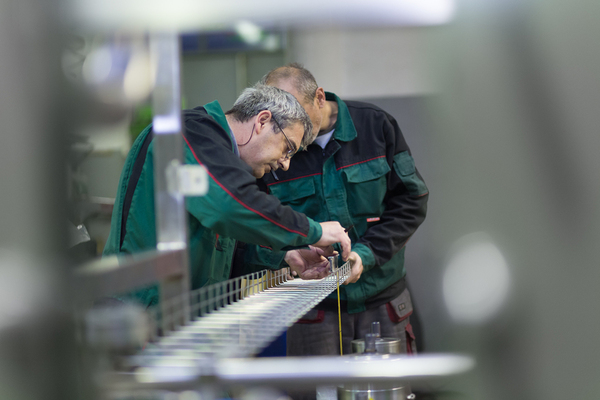
Tools and trends in digital manufacturing
Manufacturers are responding to the digital revolution in multiple ways. Each relies on the sharing and distribution of data across departments, and among partners, to better leverage new technologies.
Manufacturers generate petabytes of data about their products, operations, equipment, production processes, and use. The challenge is how to integrate that data effectively to ensure that all employees can leverage the information to make better decisions. The answer is an Enterprise Resource Planning (ERP) system that integrates data across functional areas and allows teams to work together in the same system – from sales to production to distribution and beyond. With Electronic Data Interchange (EDI), companies can share data from the ERP with other businesses, including suppliers, vendors, distributors, and customers.
Data is clearly the key and will continue to be critical as manufacturing industries use it in the following ways:
- Data analytics. More data are provided by objects in the Internet of Things (IoT), which contain software, sensors, and wireless connectivity. These devices can collect, transmit, and store data and alert people or other devices about issues, repairs, maintenance, or productivity. This collection of data gives manufacturers a clearer sense of the supply chain, and how products are moving through the factory. Multiple people can review data at the same time, and adjustments can be made to deliveries and operations to improve efficiency.
- Reducing footprint. With a better understanding of processes, companies can reduce the footprint of factories, storage, and distribution facilities. Less footprint means leaner manufacturing and reduced production costs.
- Digital technology product life cycle. Transforming product life cycles into a digital format provides greater visibility into products to streamline development. According to McKinsey, digital technology product life cycle management may help to eliminate bottlenecks like rigidly sequenced processes or complex division of responsibility between R&D teams.
- Better relationships. Data sent by users can be leveraged to improve the way products are built and how manufacturers respond to inquiries. Customers today expect connected relationships with the makers and sellers of products and are more willing to share information.
- Less complexity. Complexity can slow down processes and introduce lag that drives up costs. With cloud computing, large data sets, and real-time analytics, companies can swiftly pinpoint bottlenecks and reduce complexity in the manufacturing and distribution processes.
- Professional collaboration. Manufacturing USA (formerly the National Network for Manufacturing Innovation) is a federal program that brings together industrial, academic, and government partners to help improve competitiveness among US companies. It also provides a robust R&D infrastructure. Similar efforts are underway in Germany and China. The global Industrial Internet Consortium is focused on bringing together partners around the world to create a “securely connected and controlled” industrial Internet of Things “to deliver transformational outcomes.”
Technologies transforming manufacturing
Many technologies are leading the way for digital manufacturing. In addition to the Internet of Things (IoT), here are a few other areas where digital technology is transforming manufacturing.
- 3D Printing. By using digital designs and various resins, plastics or metals, 3D printing, also known as additive manufacturing, can make parts in small lots. In addition, 3D printing and shipping on demand can dramatically reduce downtime and reduce costs. 3D printing helps create better prototypes and reduces the time from concept to production. Some of these 3D parts are also lighter and more durable, creating efficiency gains in manufacturing, aerospace, and transportation. 3D printing can help propel innovation by accelerating the prototype process and allow for faster collaboration and testing.
- Advanced Materials. New materials are projected as being critical to solving critical societal issues and trends such as energy efficiency, resource shortages, chemical safety, and next-generation consumer devices. These materials may include advanced composites that, to date, have only been used in high-cost applications. However, advances in manufacturing processes and production efficiency may allow the use of these composites in more industries and production methods.
- Augmented Reality. Advances in computer science, computer vision, and virtual reality have allowed for more accurate work. Using goggles, employees can follow text and graphics to help do complex tasks using real-time information. The tools can assess the timing and accuracy of the work being done and improve the quality and safety on the line. These technologies can help enhance training, improve response times for maintenance, supplies, inventory management, and R&D. These technologies could also be licensed to other companies looking to improve operations and design new and better equipment.
- Cloud Computing. Connected services, applications, and data access empower employees in different functional areas, on different devices and in different locations to access, discuss, and act on the same information, all in real-time. In addition, the growth of powerful analytics programs means that data collected from disparate systems can be displayed in easily usable formats for better decision-making.
- Nanotechnology. A nanometer is one-billionth of a meter. Nanotechnology encompasses materials between 1 and 100 nanometers that can be used to make strong, durable, lightweight objects for boats, autos, sporting equipment, eyewear, and medical devices.
- Robotics. Automated manufacturing has been around for decades and has taken off in the past decade. Some critics believe that robotics actually stifles innovation by eliminating humans from the process of discovery within a particular process or product. In the United States and elsewhere, robotics is not seen as a full-replacement choice, but instead is complementing a human workforce. Known as “cobotics,” this approach is gaining momentum, allowing for innovation in complex manufacturing processes.
Are you ready for the digital manufacturing revolution?
Companies that have yet to venture into digital manufacturing need to consider several critical questions to decide whether the approach is right for their organization. C-suite executives should be asking the following:
- How will digital technologies disrupt my industry over the next five to 10 years?
- What new ecosystems will emerge as a result of that digital disruption?
- Where is the value for our company in digital transformation? How do we maximize that?
- What new skills, capabilities, platforms, technologies, and employees will our organization need?
- How will we find, assess, and select those new assets?
- How do we prioritize and implement new processes, such as the digital technology product life cycle?
- How close is the digital revolution to the doors of our factories and our board rooms?
- What investments can we make now to infrastructure and cybersecurity?
- What partnerships do we need with technology providers, with government or industry organizations, or within our supply chain?
- Where should we start? What would be a good project to test?
Systems become a critical component of digital manufacturing. Leveraging the interrelated complexity within the organization is important. By bringing together manufacturing, operations, marketing, sales, distribution, payroll, and analytics, an organization will be ready to adapt to the new technologies.
ERP brings together the data from across the organization, providing a coherent and consistent display of information on performance. The right ERP solution is a major step toward digital innovation and can put you miles ahead of the competition.
NexTec Group has over 25 years of experience helping companies select and implement ERP software. Our consultants have deep expertise in manufacturing and can accelerate your digital transformation. For more about how NexTec can help your company embrace Industry 4.0, read our free guide on 10 tips for smarter ERP selection.