Customer Success Story
EMS Adhesives
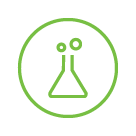
Industry
Process Manufacturing
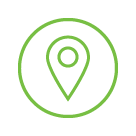
Location
Delaware, OH
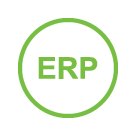
System Selected
Sage X3
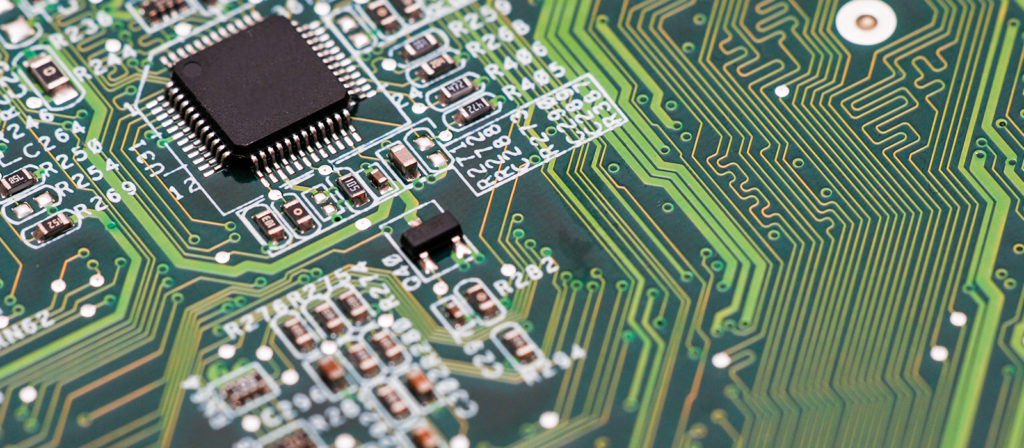
Key Results
We expected a customer-centric, customer-responsive attitude and way of doing business and NexTec has been that and more.
Their Story
As Quality Control Manager for Engineered Material Systems, Inc. (EMS Adhesives), Christina Cantrall has taken part in both production and technology improvements that cleared the path for the adhesives manufacturing company to grow over the last decade. But it hasn’t always been easy for this quality control professional. Cantrall needed to learn more about current software choices and which one would best solve the specific global process manufacturing issues her company faced. Whether it was the cobbled together software that created inventory and accounting mix-ups or employees struggling to navigate between separate systems then resorting back to manual processes in the end, Cantrall knew one thing. It was time for an upgrade.
For 20 years, Engineered Materials Systems, Inc. (EMS), has served the appliance, automotive, filter, lighting, medical, and microelectronics markets as a manufacturer of adhesives, conductives, and encapsulants. Committed to designing specific adhesives to fit their customer’s application needs, EMS is a market leader in providing innovative and cost-effective solutions for original equipment manufacturers.
“We expected a customer-centric, customer-responsive attitude and way of doing business and NexTec has been that and more.” Christina Cantrall, Quality Manager, EMS Adhesives.
An uphill battle
EMS develops products with intricate recipes requiring quality control testing and documentation at every cycle. They needed an Enterprise Resource Planning (ERP) system that understood the complexities of their industry and the quality control measures they had in place. The steady demand for state-of-the-art acrylics, epoxies, silicones, and urethanes brought EMS into a global market and their existing process technologies were not keeping up with the inventory management and accounting needs EMS continued to face. With growth came increased requirements for efficiency and visibility at every stage in the supply chain and current systems weren’t answering the call.
Climbing the mountain
The company leadership knew they needed to upgrade to a modern manufacturing ERP complete with quality control, inventory management, accounting and customer-focused integrations. Cantrall added EMS wanted something “easy to use that could house a lot of information and data… and capture the detail that we needed.”
Cantrall had previous experience with a past version of Sage software so she sought to find an implementation partner familiar with Sage’s capabilities. Sage recommended NexTec Group and a partnership was formed. NexTec representatives traveled to EMS Adhesives’ facilities and she remembers, “Our tech teams were a good fit and we felt comfortable right away.”
Prior to meeting with NexTec representatives, Cantrall admits not having much insight on the technologies available or from whom to get credible and customized direction. Rather than providing EMS with a canned solution, Cantrall appreciated the way NexTec was eager to learn of their entire operations in order to design a customized solution that went above and beyond to solve their problems. Cantrall goes on to describe how NexTec was even able to uncover and solve problems of which they weren’t fully aware prior to the partnership.
“In the end, we selected Sage Enterprise Management as our solution,” Cantrall smiles. “We had to look at users and make sure it was user-friendly so that they could navigate through the systems easily, find the information they needed be able to work at a fast pace and be efficient.”
Cantrall appreciated NexTec Group’s extensive experience with the catalog of add-ons. “They are really honest about what is appropriate for us, to meet our needs but not to overbuild. They don’t just try to sell us something with a huge price tag,” Cantrall says of NexTec’s recommendations. “But no matter what direction we go, or choice we make, they will support us either way. They seem to be focused on that customer-for-life concept.”
“We’re far more efficient on the processing side, we have a lot more capabilities than we ever did before” Christina Cantrall, Quality Manager, EMS Adhesives.
Back to basecamp
Beyond technology and systems expertise, NexTec brought customer service to a new level for EMS Adhesives. “We expected a customer-centric, customer-responsive attitude and way of doing business and NexTec has been that and more,” Cantrall appreciates. “We’re that way and it’s helpful if you have suppliers with that same focus.”
EMS Adhesives and NexTec crafted a particularly innovative way to keep their lines of communication open. By using the third-party project management and team communication application Basecamp, EMS enjoyed a somewhat informal, chat-like form of support handling often used for remote teams.
“We set up Basecamp at the very beginning of this project, so we could go back 5-6 years and look at the threads and responses. NexTec’s whole staff has access to Basecamp,” Cantrall says as she appreciates the direct line of support to a diversified set of NexTec expertise when the need arises. “It really facilitates the communication and has worked well for us. They, of course, will jump on a call, but lots of little questions can be addressed through this method.”
“They don’t hear from us frequently but respond quickly when we do reach out,” she says of NexTec support. “We haven’t encountered a situation yet where they couldn’t help us.”
After Sage Enterprise Management integration, Cantrall and EMS were more in control of operations beyond the level of detail original to their vision. “We’re far more efficient,” she’s happy to report, “and on the processing side, we have a lot more capabilities than we ever did before.”
“When we buy a product, our raw materials go into our warehouse to a ‘quality hold’ status until we confirm it meets our requirements and that it is what we ordered. We get a quality control notification for all quality holds which wasn’t an option with the former system.”
The process control system that is part of Sage Enterprise Management gave full visibility, traceability, and accountability – something required for EMS to operate in markets with high reporting requirements like the healthcare industry. “With Sage Enterprise Management,” she adds, “we have lots of visibility to the physical location and quality status of everything in our supply chain. It enables complete transparency and the ability to quickly retrieve data.”
As a result of EMS Adhesives Sage Enterprise Management implementation, Cantrall proudly offers, “We can do our jobs better, we can help our customers faster, get them information or material more quickly. Compliance is much better. There’s so much the software can do, it’s very powerful,” she states. “It’s all right there at the user’s fingertips – they can get it on their computer at home, if they’re a visiting a customer, if they’re around the world and just want some accounting detail,” Cantrall knows Sage Enterprise Management gives her users the secure access to data her operations require.
“Most can’t do what we can do easily,” Cantrall states when asked about Sage Enterprise Management’s customer-focused controls. Extremely helpful in their customer service goals, “the system allows us to set up customer-specific functions throughout. We can add or modify customer-specific reports easily and with detail.” Cantrall goes on to say, “We try to differentiate ourselves around customer-centricity. We show all the details with our products and our customers even use our system for their materials – all of which makes us a stickier vendor for them.”
A team win
Christina Cantrall concludes the EMS Adhesives upgrade story with some final thoughts: “The success of our systems is really about NexTec. We’ve been really happy with their service. They are continually growing their technical and project management ability, and are very responsive to our needs.”
“EMS and NexTec have developed a team effort as far as keeping our system integrated, operating effectively and making our people more efficient,” she remembers, “they were very supportive with upgrades, patches, additional training and enabled us to convert in a very narrow 4-month window. They have been a very good business partner.”
About NexTec Group
NexTec Group is one of North America’s largest and most experienced technology consulting firms, specializing in industry-specific solutions for mid-sized organizations. For nearly 30 years, NexTec has been a trusted partner to businesses, delivering, implementing and supporting the core Enterprise Resource Planning (ERP) solutions they need to scale and grow. NexTec is a gold-certified Acumatica partner with deep experience in field services, manufacturing, distribution, professional services, and more.