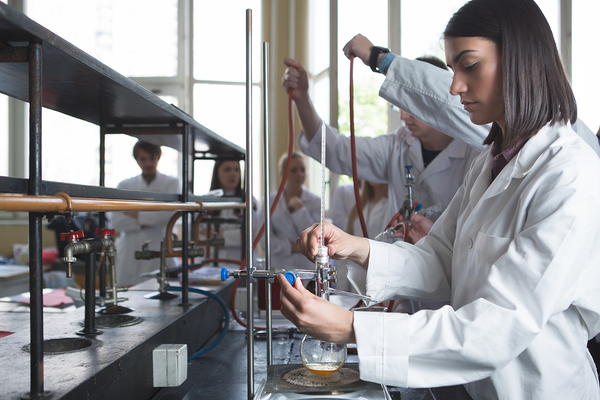
The chemical industry’s regulations and requirements are about as volatile as the chemicals it produces. Companies face strict rules and procedures to follow that are enforced by governing agencies, and any instances of non-compliance can be costly to resolve.
To further complicate the process of doing business, chemical companies must not only be aware of the dangers of the chemicals they use, handle and produce, but also the resulting impact on the environment, safe handling and shipping procedures and long-term occupational risks and hazards to employees.
Because of the very nature of the chemical industry, choosing an Enterprise Resource Planning (ERP) system to manage the unique intricacies of chemical manufacturers requires firsthand expertise of the challenges and needs of the industry. Multiple layers of complexity must be taken into account when vetting solutions that can help companies manage product, personnel and compliance needs alike.
The following steps can help to guide the selection process and ensure you gain the most value from your investment:
1. Review Important Chemical Industry Challenges
Because of the dangers and volatile nature of the chemical industry, manufacturers face many challenges not experienced by other industries. Aside from stringent health and safety requirements and compliance regulations, chemical producers must also contend with fluctuating fuel costs, power usage, equipment maintenance and replacement, operational costs, logistics and other hurdles that can affect profit margins.
There are myriad of moving parts to any chemical manufacturing business. Companies who are seeking a comprehensive solution to gain greater insight into operations will need to consider material management, finance and accounting, shipping and receiving, planning and production, customer service, sales, marketing, and company leadership roles, and understand how an ERP solution can cater to each of their needs in an efficient manner.
This is why it’s essential to choose an ERP that’s designed to help companies overcome these and other challenges. One size fits all systems aren’t designed to address the underlying needs of chemical companies, but rather general challenges experienced by all industries. In addition, the providers deploying a generic ERP may also lack the expertise and understanding required to help you successfully launch your ERP and provide ongoing support when needed.
2. Consult with Key Team Members
ERP systems are often leveraged across the organization, which means that each user’s needs and priorities should be taken into account. These may include, but are not limited to:
- Company leadership
- Development teams
- Sales and marketing
- Warehousing
- Shipping and receiving
- Transportation providers
- Customer service representatives
- Production teams
- Materials management
- Procurement
- Financial and accounting personnel
- Data management
- IT department
- Other parties in the supply chain
Determine who will benefit from a chemical industry ERP system and the data or other details they need to know to better perform their roles. For example, chemists can use ERP to accurately record and manage product formulas, while procurement departments can log the vendors and cost of each material used in the formula for easier ordering and improved financial records.
Also, it’s important to look at an ERP system from a usability standpoint. Determine how each key team member will use the system, how long it takes to implement the solution and the overall learning curve to confidently use the new system.
3. Conduct a Scalability Test
There’s a lot more to choosing a chemical ERP system than being able to check all the boxes on your requirements list. You must also consider, to the best of your ability, long-term needs and business objectives. As your business grows and undergoes changes, your ERP should be designed to adapt to your company over time. Otherwise, you may find yourself going through the exploration and comparison process all over again (and spending more than you really need to in the process!).
Not all ERP systems offer the same level of scalability and flexibility, though it’s becoming more common to adapt ERP systems to future needs. If you believe you might outgrow your ERP in the next five to 10 years, it’s best to continue exploring options. A “bad” ERP may end up preventing your growth instead of supporting it.
4. Determine the Need for Third-Party Integrations
Part of an ERP system’s flexibility lies in the ability to customize the system to your unique needs. As a general rule, chemical ERPs are designed specifically for the industry, yet there may be many instances where companies will need greater control over how their ERP looks and functions.
A lack of or limit on customization is a major obstacle you’ll be glad to avoid. Companies who discover that they can’t customize a certain feature are often forced to turn to third party integrations to perform a task or function.
While this isn’t necessarily a deal breaker, consider that too many integrations and workarounds can often bog down processes and muddy your system. And when one workaround no longer works, you’re forced to integrate additional solutions that only make your system more complex.
In addition, too many “bolt-ons” can lead to confusion when new team members are brought on board, particularly in the IT department that’s tasked to help manage and maintain the system.
Though there is no magic number as far as integrations, it’s important to consider ahead of time the ERP’s flexibility (or lack thereof) and understand how it might impact your system and total cost of ownership over time.
5. Investigate Product Support
All ERP systems come with some level of product support, but this can vary widely by platform and provider. Implementation is only the beginning when dealing with an enterprise-wide system like an ERP. Aside from the initial launch, you may also require ongoing help and support during onboarding, as well as when training new employees, making major updates to the system and changing as your business grows or adapts to changes in the marketplace.
In addition, you should consider the way in which support is delivered. Some vendors may provide limited free support via phone, or direct you to an online knowledge base or FAQ for answers to your questions. Others may offer paid support packages that provide phone and chat services for a fixed monthly fee. This is something that should be considered in your overall cost of ownership (more on this in Step 7) to ensure the ERP fits within your budget requirements.
6. Check Technology Requirements
Will you deploy an on-premise ERP or take advantage of cloud technology (or even explore a hybrid model)? Do you have an on-site IT team that can create and manage the infrastructure required to operate your ERP? Is your internet connection strong enough to support a cloud-based solution? Will you provide mobile devices to your employees who need mobile ERP access?
The technology requirements can have a lot to do with the ERP solution you implement, especially when it comes to investing in infrastructure and devices. There is no single best solution when it comes to hosting, as what works for one company may not work for another. Consider the technology requirements and their associated costs when weighing your options to stay on task and on budget.
7. Consider Long-Term Costs
It’s easy to consider only the upfront costs of your ERP for the chemical industry, but as with all major business purchases, it’s important to also consider long-term expenses. Aside from the initial investment, chemical companies will also be tasked with maintaining their ERP systems, costs of implementing changes as you grow, upgrading technology requirements and training and onboarding for new employees.
As a rule, your ERP should be set up to reflect your long-term business objectives. As your processes and operations evolve, your system and vendor should be able to evolve with you to continue delivering on your objectives.
8. Add the Mobile Aspect
As this past year has shown us, understanding the mobile capability of an ERP is critical. Not all employees need to be chained to a desk to conduct business (particularly in outside sales and logistics), so giving them the freedom and flexibility to work from anywhere can help to boost productivity, improve morale and better serve your customers.
ERP dashboards are becoming increasingly mobile friendly, with many solutions offering apps specifically designed for mobile devices. Key employees can collect data while in the field without having to perform double data entry upon returning to the office. This can also reduce the potential for errors and allow employees to better utilize their time.
How to Create Better Opportunities with the Right ERP for the Chemical Industry
The right ERP system can be a central anchor point for your entire organization, helping to turn chaos into control and breaking down the dreaded silos that plague productivity and collaboration.
And even with a chemical ERP made to address the unique challenges and needs of the industry, requirements can still vary by company. For chemical manufacturers, NexTec recommends Sage X3. Our software is configured by our industry experts to address the unique challenges of the chemical industry. Our goal isn’t just to implement an ERP, but also help you discover the best system to streamline processes, build efficiency into your operations and benefit all users within your organization — all within your budget.
For more information on how Sage X3 and NexTec could work for your chemical business, reach out to us. We’d love to chat.
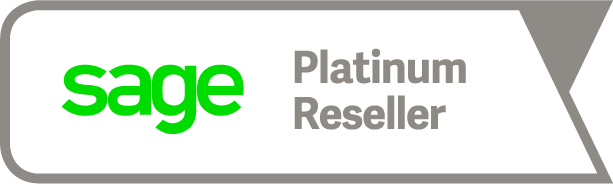