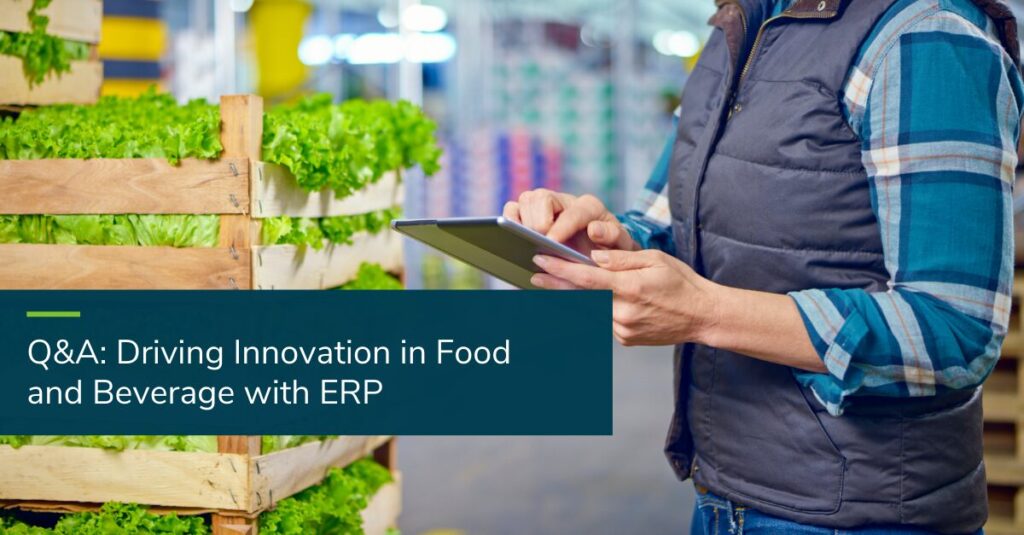
NexTec recently sponsored “The State of Innovation in Food Manufacturing” virtual event co-hosted by Food Dive and Manufacturing Dive. The replay of our featured session “Driving Innovation in Food & Beverage with ERP” is now available on demand.
In this 20-minute Q&A session, Sharon Fuchs, Solution Architect and Mark Pileski, VP of Marketing at NexTec Group discuss how digital innovation and advances in ERP software such as AI and predictive analytics enhance efficiency, ensure compliance, and drive sustainable growth.
“One of the core features or benefits of how ERPs streamline operations always comes back to cost and compliance,” says Fuchs. “We can reduce our costs by minimizing errors, reducing usage, and preventing overproduction or underproduction. Accurate forecasting gives us better production and output. At the end of the day, ERPs are powerful systems for modern food manufacturing companies that help them stay competitive in a very, very fast-changing market and industry.”
Watch Now
View the webinar replay or read the full transcript below.
Full Transcript
Mark: Good day, everyone, and welcome to our “Driving Innovation in Food and Beverage with ERP” session. I’m really excited to join this event and happy to say that I’ve got Sharon Fuchs with me – we go back over 10 years in building and implementing solutions for the food and beverage industry. Sharon, tell us a little bit about your experience in food and beverage.
Sharon: Hi Mark, thanks for having me. You’re right, we’ve been together a long time, but I’ve been in this industry, I would say 20-ish or more years in ERP, specifically focused on food and beverage. I had a small break in an organic natural food business where I was a buyer within that cycle. So, I’ve been doing this for a long time.
Mark: Well, we appreciate you joining us today. Thank you for taking the time out from whatever random hotel you’re in today as you travel all over North America implementing these solutions. Today we’re going to talk about driving innovation in food and beverage with ERP. But before we get into the discussion topics, maybe share for some of the audience what ERP is and when would an organization consider using it?
Sharon: An ERP is an Enterprise Resource Planning tool. Think of it as exactly that, a tool for an organization where it brings together integrated data. So, from an organization, if you’ve got siloed or disparate systems and you’re looking to understand your cost and the quality and compliance of the product that you’re making downstream, and where everything lands, you’d want to consider an ERP application for your business. And there’s a number of them out there that serve that industry niche.
Mark: Typically, at what maturity level would someone have to consider an ERP?
Sharon: That’s a tough question. I mean, I’ve worked with startups. I’ve worked with companies that have been at it for 3 to 5 years and then companies that have outgrown Excel 10- or 15-years in. It depends on when the company’s ready. It’s really the appetite and the projected growth and strategy of the company itself.
Mark: Great. Thank you for that, Sharon. For today, we’re going to talk about how ERP can streamline operations and supply chains, how organizations have leveraged automation for smarter decision-making, and how an organization would meet regulatory and sustainability goals using ERP and technology. And these are all from examples that Sharon has implemented across North America over her career. We’re lucky to have her. Let’s jump right into it, Sharon, and start talking about how ERP streamlines ops and supply chains.
Sharon: Absolutely. There’s a number of points that come into play here. Let’s just start with the ERP itself. It acts kind of like a centralized hub. It integrates departments within the business unit – procurement, production, sales, finance, distribution, and so on. Some companies I walk into, they’re running their own independent CRM. They’re taking orders in the CRM and then they email the work order or the need or the demand to production. Production looks at what they need to make. They’ll communicate to procurement. Procurement looks at the inventory, the low levels. They’ll validate that in an Excel sheet. Quality is doing something sort of off to the side.
What the ERP does is it brings it all together in one cohesive platform. I like to explain it like this: we’re under the same roof. We all live in the same house. We may work in different rooms, but at the end of the day, we understand what’s going on because we can hear the chatter in the background, or we can see what’s going on in the kitchen.
When you look at how ERP can streamline operations, there’s enhanced inventory management. Manufacturers are typically dealing with highly perishable goods with expiration dates, batch numbers, unique storage requirements, maybe certifications around those storage requirements. So that ERP system really provides real-time inventory tracking.
“ERP doesn’t replace employees. It’s not typically meant to reduce the workforce. It allows your employees to make better strategic decisions within their business units. It offers real-time data analytics, insights into bottlenecks and inefficiencies, and how we can optimize workflow, which leads to faster production cycles, reduced downtime, and overall, higher productivity.”
– Sharon Fuchs, Solution Architect, NexTec Group
It helps companies monitor their stock levels and predict demands by using features like automated reordering, first expiry, first out from an inventory perspective. Even tracking lot-level detail right in the product, like a bricks level. For example, at a sugar level and the ability to commingle multiple bricks levels or lots to get to that end spec. At the end of the day, it can reduce waste, it can reduce spoilage, it can reduce rework.
Building on that, you get improved traceability and compliance. I mean, FSMA is right around the corner. That Food Safety Modernization Act is coming into play. Most companies are GMP, HASSA, SQF, BRCGS, or all those certifications that align with the food and beverage industry.
In terms of how an ERP can help streamline compliance, it will allow manufacturers to track products from raw materials to finished good, to rework, to buy products, to co-products, ensuring a quick response to – I don’t like the word recall – so I call them traceability exercises to prove compliance. And that window is really shortening. I keep hearing four hours and some companies are demanding two hours. It’s really a prescribed amount of time that we have to prove compliance. With ERP, we have the ability, because we’re tracking those details, to meet those safety certs, those requirements that the standard in the industry is demanding of us.
Streamlining procurement is another way that ERP systems help streamline operations. So, what is it? It’s the ability to automatically reorder product. Our production schedule is two weeks out or three weeks out, but maybe our longest lead time is eight months out, or we’re bringing product in from overseas or in containers, right? So, it will help with the planning from a procurement process and to ensure that raw materials arrive in time. It will help reduce the storage costs, avoid delays in production. And production can see if there’s an expected receipt date change that triggers that domino effect. So, production can see that data and make the necessary adjustments. We may have to air freight the product in, or resource it, or whatever that looks like, but it gives them that visibility within the application.
Obviously, what that leads to is operational efficiency by automating those repetitive tasks like data entry, order processing. If we’re not scripting out what those lot numbers are or, you know, we have the ability to do it on a terminal or a tablet or a handheld, it increases or betters that operational efficiency and frees up employees to focus on strategic activity.
ERP doesn’t replace employees. It’s not typically meant to reduce the workforce. It allows your employees to make better strategic decisions within their business units. It offers real-time data analytics, insights into bottlenecks and inefficiencies, and how we can optimize workflow, which leads to faster production cycles, reduced downtime, and overall, higher productivity.
At the end of the day, one of the core features or benefits of how ERPs streamline operations always comes back to cost and compliance: how do we reduce our costs?
We can reduce our costs by minimizing errors, reducing usage, and preventing overproduction or underproduction. Accurate forecasting gives me better production and output. I’m avoiding waste, and I get better specs.
When we have more lot-level visibility in terms of if our ingredients and our raw materials have varying degrees of potency or levels that can affect our production process, we can see that and make decisions based on that. At the end of the day, ERPs are powerful systems for modern food manufacturing companies that help them stay competitive in a very, very fast-changing market and industry.
Mark: Awesome. Thanks, Sharon. It’s always amazing to me some of the customers we’d come across and how they would be managing things on an Excel sheet and on these homegrown systems and how a recall could just blow the entire operation up. It’s amazing that there’s technology available and people who can help with that. Let’s move on to leveraging automation for smarter decision-making. I’d love to hear what you have to say on this.
Sharon: So, keep in mind, if you’re working within a facility and it’s all paper today, don’t think that an ERP implementation must be full-blown automatic scanning… Just to be clear, you can crawl, walk, run, and get to that end state, but you don’t have to do it full bore out of the gate.
But how do we leverage automation to make better decisions? You know, ERP can give you real-time data insights, right? So, what does that mean? You can automate ERP systems by continuously gathering and processing data from across your organization. So, across inventory levels, production rates, and sales figures, this can eliminate delays caused by manual data entry. Waiting for the information, waiting for the production reports to come up from the day before, giving you real-time analytics into your organization. Let’s say you’re seeing some spikes in demand for a product: you have the ability to adjust. And sometimes customers cancel orders. And if we’ve got that product slated on the floor to be made, we have the ability with ERP to adjust that schedule so we can reduce waste and increase efficiency.
You’ll start to hear about predictive analytics, right? AI, artificial intelligence, is sort of coming into the forefront. It’s still a bit out there. We still need to understand it better, and it still needs to prove itself, but it is making a mark. You’ve got machine learning algorithms within the system, so ERP systems can take that data and use AI to analyze it. It can identify patterns that people might miss. For example, you can predict seasonal fluctuations in demand or pinpoint inefficiencies in a production process. You know, this foresight really enables food manufacturers to proactively address any challenges like ramping up for production ahead of a seasonal surge, switching suppliers before a disruption, or mitigating impact from an operational standpoint.
You know, in addition to that, it’s going to improve quality control from an automation standpoint. So, sensors in machines, you know, they call it IoT or Internet of Things. They have sensors that you can integrate into the production process. And they can gather information like temperature, humidity, and equipment performance in real time. You can marry that data to production efficiency and quality. Those quality checks can be used to identify defects or anomalies during the production process or pre- and post-production. By that, it would prevent subpar products from reaching the consumer. This not only enhances quality, but it reduces waste and supports compliance with those stringent food safety standards coming more and more into play.
That improved quality streamlines operations. You can automate routine tasks such as order entry and inventory updates in the procurement process. It removes bottlenecks and ensures consistency. For example, when our inventories drop below a certain level or threshold, we can have the ERP automatically generate and send a PO to our suppliers. It eliminates the risk of delays caused by human oversight and ensures that the raw materials are here when needed. There’s so much going on in those facilities. There are so many balls up in the air and things that they’re juggling. It just helps to create a sense of stability within the organization.
That obviously leads to enhanced traceability and compliance. Within the food industry, traceability is a cornerstone for any organization. It’s critical to meet that regulatory requirement and maintain consumer trust in the brand, or if you’re an ingredient manufacturer and you’re making products for other companies – so, very high standards of compliance and trace. How does an ERP serve that? Automating ERP systems can track products from raw material, byproduct, rework, to finished good. Rework is important. And if that’s a part of your process, we can capture that. You can maintain it. You can cost it. And more importantly, you can understand where that rework goes and what that goes into, what it gets converted into, and ultimately who it gets sold on to. That whole chain of command lives within the application. In the case of traceability exercises, it allows manufacturers to quickly identify affected products, remove them from distribution, follow the proper chain of communication, and minimize that risk to the organization and to the folks that have it in their pantry, their fridge, or on their shelves.
Cost optimization is another way that ERP supports the process. Automation can help identify areas where resources can be used more efficiently. For example, ERP systems can help analyze energy across production lines and recommend adjustments to reduce consumption. They can optimize raw material usage and suggest best combinations. I was just in a facility last week and they do a lot of fresh cutting and processing. The onions are at the end of the season. They’re waiting for the new harvest to come through. So, they’re a little bit older, there’s less yield on them because they’ve been sitting in storage. You can actually have another version of that bill of material that serves that time period for that product that you’re using to then align with yield analytics and costing so you don’t have these crazy variances from a reporting standpoint. More importantly, you know what you need from a usage perspective.
Mark: To be conscious of time, I want to make sure that we cover the final question on meeting regulatory and sustainability goals with technology.
Sharon: When we look at regulatory, in my world, all roads lead to finance and compliance. As we look to regulatory systems, you’ve got traceability, automated quality control, and digital documentation. Traceability, we need to understand the cost and the spec from a safety cert of where that product’s coming from so manufacturers can trace the batch, the product back to whether it’s the farm, the vessel, the vendor. Knowing where that came from gives you that core compliance. Automated quality control. You’ve got sensors that control temperature and humidity. You’ve got an internal process, which governs the receipt of product, compliant…you know, aligning it with when it’s received on the dock, goes into a quality hold, quality verifies that it aligns with the spec.
And then as we go through those in-process inspections, we can validate that the product is safe, but it also manages the facility and safety of the facility, right? In addition to product, it’s temp checks on the line. It’s validating washing stations. It’s making sure that we’re doing time-based audits or inspections on the metal detection. Compliance is not just product-specific. To me, it’s holistic across the facility and the product that we’re working with. And then ultimately that digital documentation aligns with the ability to store vendor certs, any SOPs that need to be made available to different people at different times.
Sustainability goals. We hear that a lot. So, creating energy efficient facilities, reducing waste and looking at our sourcing. From an energy efficiency, you’ve got smart manufacturing systems that can leverage different tools for energy consumption so you can align it with usage patterns and adjust equipment schedules to operate maybe during off-peak hours, if that’s even an option. Waste reduction by analyzing inefficiencies that can lead to waste, such as overproduction or spoilage. First expiry, first out, product management. That lives within an ERP system. Sustainable sourcing as we look to certifications, whether it’s fair trade, whether it’s organic. There’s a number of certs, B Corp, that align with sustainable sourcing practices that can all be managed and maintained within the ERP. And documents and transactions can be blocked if the certs aren’t up to date. Things are put on hold or blocked if the certs aren’t up to date.
And ultimately, data-driven decision-making using predictive analytics and scenario planning builds consumer trust. It builds out the ability to forecast future scenarios from a manufacturing standpoint to predict seasonal demand, maybe, for specific products. And at the end of the day, it’s about consumer trust and transparency. When you look at labeling and certifications that the consumer market is looking for within the organization, those ERP systems can help support that process.
Mark: That was awesome. Real quick about NexTec: We’re Sage’s largest and most established X3 partner that serves food and beverage in North America. Please reach out to us. We’ve got a purpose-built solution for food and beverage called FoodBusiness ERP. Look out for Sharon and I on LinkedIn. We’d be happy to talk and connect you to people to help out with your problems. Thanks, Sharon. Thanks, everyone, for your time today.
Ready to Take the Next Step?
To learn more about how a food and beverage-specific ERP solution can benefit your business, or to schedule a demo of Sage X3 and FoodBusiness ERP, get in touch with our Food & Beverage experts.