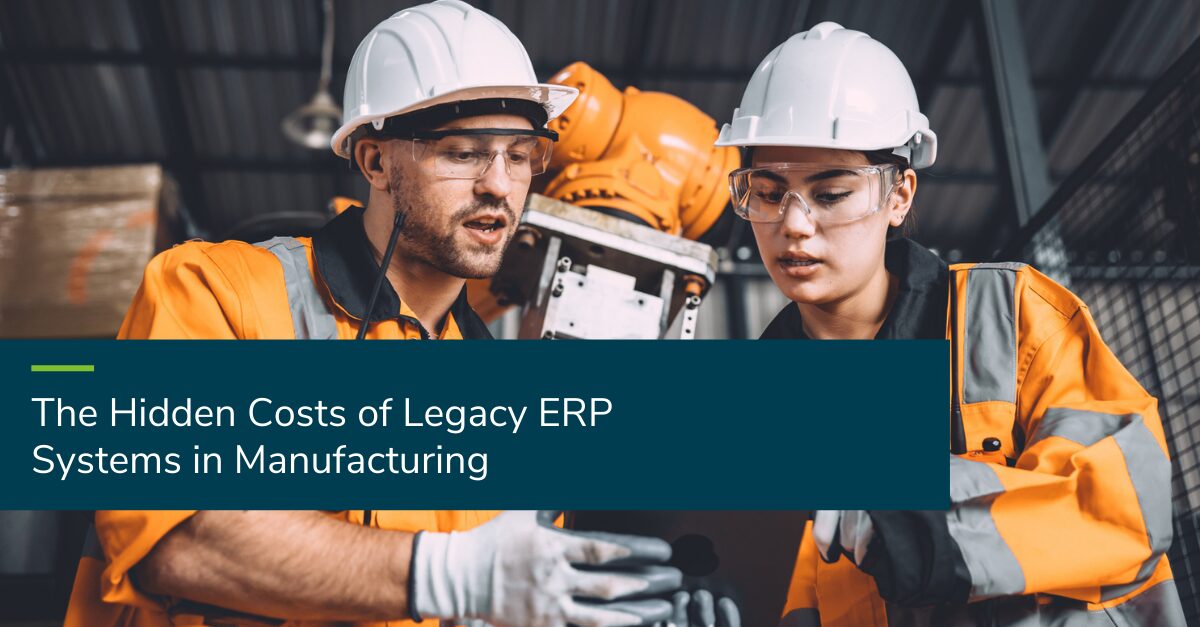
In the rapidly evolving manufacturing landscape, staying ahead of the competition often means reevaluating the tools and technologies that drive your business. One tool that might not get enough attention is your Enterprise Resource Planning (ERP) system. Our latest guide examines the hidden costs of legacy ERP systems and their impact on your ability to meet modern manufacturing demands. Choosing to hold on to an outdated legacy ERP system past its ‘best before’ date can have serious implications for your business, quietly chipping away at your efficiency, competitiveness, and bottom line.
Understanding the Impact & Costs of Legacy ERP
It’s crucial for businesses to recognize the hidden costs of legacy ERP and accounting software and consider the strategic advantages of upgrading to modern solutions. These costs aren’t just financial; manufacturers commonly face reduced efficiency, scalability issues, friction in processes and workflows, and barriers to meaningful innovation. Issues with clunky legacy ERP systems can also impact team morale and your ability to attract new talent. Our guide highlights several critical areas where legacy ERP systems can drain resources:
- Maintenance Expenses: Older systems need more care and can be expensive to keep running.
- Operational Inefficiencies: These old systems often mean more manual work and mistakes because they don’t integrate well.
- Decision-Making Delays: When your data processing is outdated, it can slow down making important business decisions.
Best Practices for ERP Transition
To ensure a successful upgrade from a legacy ERP system, it is essential to plan carefully and involve everyone who will use the new system. This not only helps in tailoring the system to meet specific organizational needs but also facilitates a smoother transition, minimizing disruptions to daily operations. To make sure your upgrade goes as smoothly as possible, consider these best practices for transitioning from a legacy ERP:
- Comprehensive Needs Analysis: Thoroughly assess current and future needs to determine essential features and functionalities in a new ERP system.
- Vendor Evaluation: Select a vendor not only based on the software but also on the support and training they offer to ensure a smooth transition.
- Employee Engagement: Involve employees from various departments in the switch. This makes sure the new system works well for everyone’s actual day-to-day needs.
- Phased Implementation: Implement the new system in phases to minimize disruption and allow time for adaptation and troubleshooting.
Take the Next Step
Ready to dive deeper into how legacy ERP systems are silently draining your resources and undermining your ability to grow and thrive? Our comprehensive guide, “The Hidden Costs of Legacy ERP Systems in Manufacturing”, offers a detailed exploration of the challenges and steps you can take to mitigate those costs. Download your copy today and begin your journey towards a more efficient manufacturing environment. Reach out to us if you have any questions!