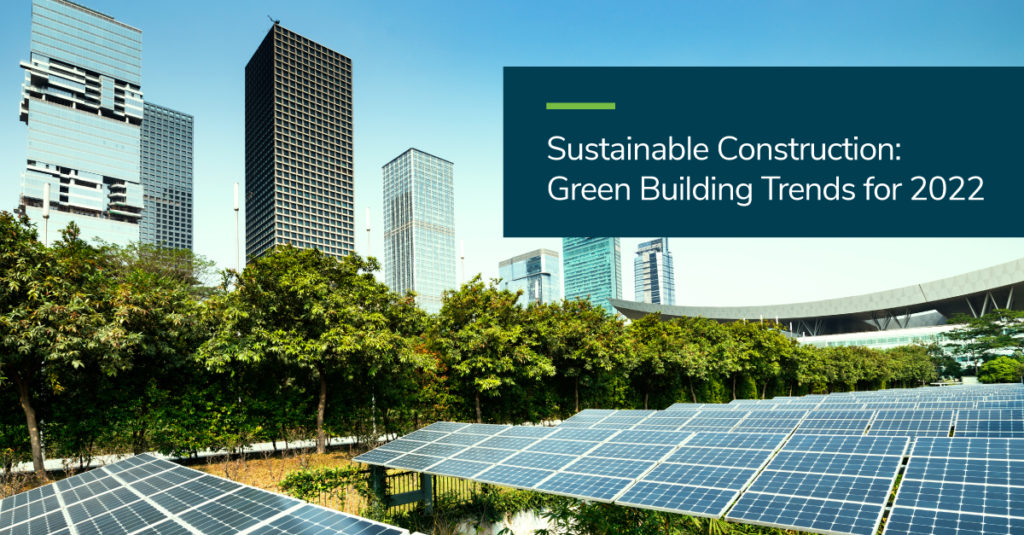
In 2018, the Environmental Protection Agency (EPA) reported that construction and demolition materials produced 600 million tons of waste—90% from demolition and 10% from construction. Though the EPA hasn’t updated the report, past statistics indicate construction waste is growing, not declining. As millions of people around the world celebrated World Environment Day — a 48-year global effort to save our planet—on June 5th, construction businesses are waking up to the fact that they have the responsibility and the power to reduce their environmental impact.
And their awakening has sparked a number of green building trends for 2022.
3 Green Building Trends for 2022
- Sustainable/Green Materials and Eco-Friendly Upgrades
- Smart windows that simultaneously protect against heat loss and increase heat retention (depending on the season) while also boosting natural light exposure, reducing energy costs.
- LED light bulbs as energy efficient lighting.
- Natural products, such as sheep’s wool and hemp, for insulation.
- Modular Construction
- Recycling/Reusing of Waste Materials
Sustainable or green materials are readily available. According to the Sustainable Living Association, the three most environmentally friendly building materials are bamboo (versatile, durable, and regenerates quickly); recycled steel (necessary building material that can be repurposed rather than created, which uses a lot of energy and resources); and sheep’s wool (all-natural, long-lasting insulation that absorbs more heat and moisture than man-made insulation). Other green materials include composites, stone, fiber cement and fiberglass.
These green materials are excellent options for sustainable construction, but construction companies are also using similar materials—along with smart technology— as eco-friendly upgrades to older buildings. For example, they’re utilizing smart thermostats to automatically modify temperature settings, which saves energy, and solar panels as clean renewable energy sources.
Additional eco-friendly upgrades include:
The result is a reduction in greenhouse gas emissions, less biodegradable waste and a decrease in construction companies’ carbon footprint. And because the majority of consumers are pushing construction companies to incorporate green-building practices, those that do so are setting themselves up for success.
Modular construction has been around for decades, and it’s growing in popularity. The designing, building and assembling of building components take place in a factory, and the components are then transported to the jobsite where they’re fitted together using cranes. Because modular construction is performed in a “controlled environment,” materials not used in one project can be used in another project within the factory, reducing material waste.
Additionally, modular construction requires less heavy equipment, modular buildings can be dismantled and reused in a different location, and, according to Unsustainable Magazine, modular construction encourages delivery optimization, reducing the environmental impact. “Overall, modular buildings require 90% fewer site deliveries, with a resulting drop in carbon emissions. Transportation emissions are a huge part of the impact construction has on the environment, so an increase of efficiency in this area has a huge effect on the overall sustainability of the construction industry.”
The recycling and reusing of materials is a building block of the environmental movement. With demolition debris being the biggest supplier of waste, it makes sense that construction companies are seeking ways to recycle and reuse materials from deconstructed buildings.
The EPA discusses the importance of deconstructing buildings in “Best Practices for Reducing, Reusing, and Recycling Construction and Demolition Materials”:
Disposal of C&D materials wastes resources and landfill space and results in pollution when new building materials are manufactured in their place. Deconstruction can be applied on a number of levels to salvage usable materials and significantly cut waste and reduce disposal. This can range from reusing an entire structure or foundation, to select assemblies and systems, to the careful removal of specific materials or items for reuse.
Sought after materials from deconstructed buildings include unique woods, hardwood flooring, multi-paned windows, architectural moldings, plumbing/electrical fixtures and brick. Recycling and reusing these materials not only significantly reduces the amount of waste being sent to landfills, but it also provides business and employment opportunities, with the waste management market growing parallel with the sustainability efforts of the construction industry.
Sustainable Construction with Cloud Construction Management Software
The construction industry is expected to grow by 8.8% and reach USD 1,355,097 million in 2022. This growth is excellent news for construction companies, but they’ll need to continue improving their sustainability practices if they want to benefit. If implementing or maintaining eco-friendly practices feels like an overwhelming task, there’s technology that can help. Cloud construction management software, such as provided by Acumatica Cloud ERP, provides construction companies with a comprehensive solution designed for their specific needs.
Cloud-based ERP software makes managing and executing projects easy by linking business-wide data into a centralized database, which is accessible anytime, anywhere, and on any browser-enabled device. Construction companies can also track and control costs, identify problems early, keep everyone on schedule, organize documents and—very importantly—manage their sustainability programs effectively.
To learn more about how Acumatica and Acumatica Construction can help construction companies achieve their sustainability goals, contact our NexTec experts. We’d love to chat.