As the world’s population continues to age and subsequent healthcare costs continue to climb, the medical supplies and devices industry is finding itself in a unique position. While there is a tremendous opportunity for industry growth and profitability, intense competition and strict safety regulations put significant pressures on businesses to optimize operations and cost management processes.
In 2020, the medical supplies and devices industry was dominated by the COVID-19 pandemic. Demand for supplies used to treat the virus specifically – such as Personal Protective Equipment (PPE) and ventilators – soared, while the overall drop in global economic activity negatively affected revenue streams for many other medical manufacturers. Supply chain issues linked to government-mandated lock-downs and trade restrictions created shortages in supplies needed to make medical devices.
Fortunately, revenue recovery is expected to increase in the second half of 2021. To ensure post-pandemic success, medical supplies and devices manufacturers need to be aware of the following industry trends and how best to capitalize on them.
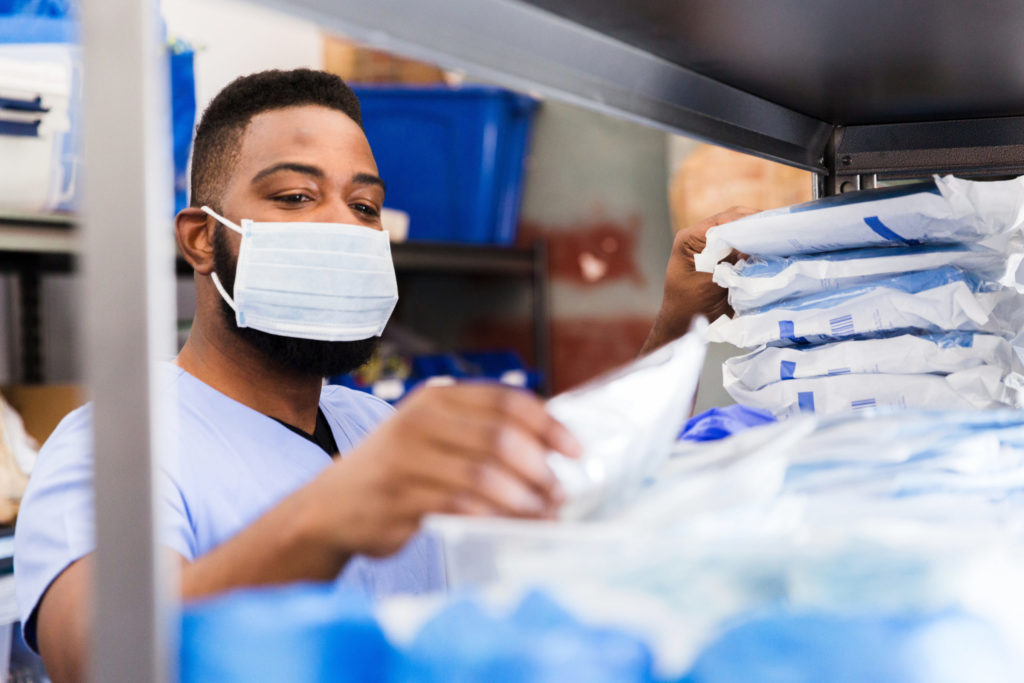
2021 Trends in Medical Supplies and Devices
Below, we look at three major industry trends that will have both short-term and long-term effects on medical supplies and device manufacturers.
Trend #1 – Big Data
Though Big Data is not a new concept, it is still a relatively new business practice. Big Data refers to the technology and practice of working with data that is large in volume, quick in speed and has many forms. For these reasons, companies are continuing to struggle to get value from the data they have access to.
In the past, Big Data was only accessible to multi-national medical suppliers, though recently it has become more available to companies of all sizes. This is due to an influx of technology tools that make data collection and analytics more affordable and accessible.
For medical supplies and devices companies, Big Data provides more informed analytics to help businesses adjust their supply chains based on demand and adapt operations to accommodate customer needs. This not only helps keep costs low but also reduces the time it takes to manufacture and deliver products to customers.
Capitalizing on Big Data with ERP
Enterprise Resource Planning (ERP) software is a centralized business management platform that connects data, departments and processes into a single solution. One of the goals of ERP software is to provide users with a 360-degree of their business for increased insight, visibility and control. By harnessing the power of Big Data with an ERP system, business leaders can track the metrics that really matter and make better, more informed decisions based on real-time inventory, warehouse and financial data.
Trend #2 – Process Automation
Automation as a trend has been dominating the medical industry over the past few years with no sign of slowing down anytime soon. Leading medical supplies and devices manufacturers are increasingly moving towards orchestration – the system of consolidating processes and workflows – using automation tools because of a number of benefits, including streamlined inventory and warehouse management.
For medical supplies and devices businesses, workflow automation helps ensure operational efficiency, product safety and profitability. By eliminating manual inventory counts, for example, and automating processes at receiving, processing and distributing, a business can better control its inventory across geographically dispersed locations without losing track of costs.
Capitalizing on Process Automation with ERP
With purpose-built ERP software, medical supplies manufacturers can automate tedious tasks such as inventory picking and packing, which helps save time and ensures products are delivered to customers faster and with greater efficiency. With the help of ERP software, medical supplies companies can also automate:
- Expiration date tracking
- Serial and lot number traceability
- Waste management
- Warehouse transfers
- Item location
- Shipment logging
By automating these processes and workflows, medical supplies and devices companies can also improve productivity and customer service.
Trend #3 – Reducing Supply Chain Costs
As costs continue to escalate in the US healthcare industry, focus is being put on how to streamline the supply chain to improve its efficiency and reduce associated costs. The healthcare industry has lagged behind other industries in terms of implementing advanced supply chain logistics and just-in-time inventory, and as a result, the supply chain as a whole is complex and often deemed inefficient.
On top of this, rising tariffs placed on products and materials going into and out of the US has further affected the medical supplies and devices supply chain, straining many businesses’ bottom lines.
To ensure profitability, medical devices and supplies companies must have the ability to operate efficiently and reduce costs throughout the supply chain.
Capitalizing on Cost Reduction with ERP
ERP software designed for the medical supplies and devices industry helps streamline the supply chain, from purchasing and inventory to manufacturing and distribution. With increased visibility and control into the production process, business leaders can improve forecasting, minimize waste and ensure efficiency every step of the way.
With complete control of manufacturing processes, for example, users can make decisions on labor resources based on real-time data from the shop floor. With visibility into bottlenecks that may be occurring, it’s easy to create better schedules, optimize production and keep labor costs under control.
Acumatica ERP – A Single Platform to Manage your Medical Supplies and Devices Business
Finding efficient ways to adapt operations and processes based on industry trends can help companies remain competitive and improve their bottom lines. To gain insight into business-wide data, streamline operations and reduce costs, leading medical supplies and devices companies turn to Acumatica Cloud ERP.
With Acumatica, medical supply and devices companies can:
- Manage business processes from end-to-end, including accounting, purchasing, sales, distribution and more
- Manage inventory with real-time visibility into quantities and costs
- Track financials
- Gain full traceability for regulatory compliance
- Scale operations and identify ways to save money
To learn more about Acumatica, contact NexTec Group’s consulting and industry experts. As an Acumatica Gold-Certified Partner and one of the largest Acumatica teams in North America, we are ready to help you take control of your medical supplies and devices business. Reach out to us for more information. We’d love to chat.