Customer Success Story
Columbia Chemical
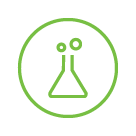
Industry
Chemical Manufacturing
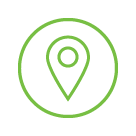
Location
Brunswick, OH
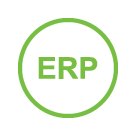
System Selected
Microsoft Dynamics GP
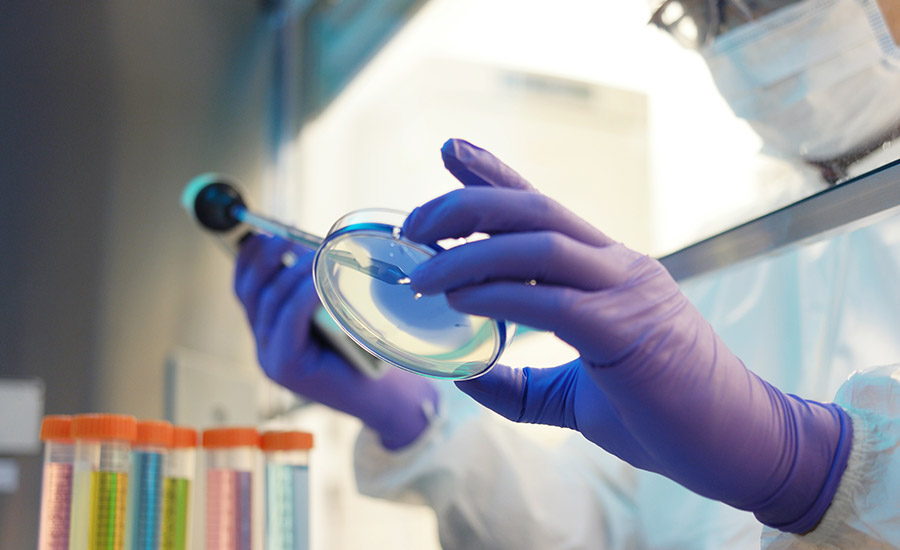
Key Results
We give NexTec a lot of credit for the success of this project—the chemistry just worked.
Their Story
Columbia Chemical has always operated on the cutting edge of technology in the metal plating industry. More than thirty years ago, the company pioneered an environmentally friendly alternative to cyanide-based zinc coating. To manage its financial, inventory, and manufacturing operations with state-of-the-art precision, Columbia Chemical selected Microsoft Dynamics GP, Vicinity Manufacturing, and the technical consulting services of NexTec Group.
“We invest in technology to help us develop better and safer products,” says Kevin Reilley, vice president of operations for Columbia Chemical. “When it was time to apply that same thinking to our business software, we turned to NexTec.”
Invest in an end-to-end solution
Columbia Chemical previously used Peachtree by Sage to manage its core accounting, but inventory control, batch processing, quality control, and governmental compliance tasks were all handled manually. “There was a lot of paperwork, duplicate entry, and time spent maintaining spreadsheets,” recalls Reilley. “We knew that in order to continue to grow the business we needed a true ERP and manufacturing solution. We needed a solution that could address our core accounting, distribution, and specialty chemical manufacturing requirements.”
A detailed request for proposal returned three different options: Sage MAS 500 ERP, Microsoft Dynamics NAV, and Microsoft Dynamics GP. Reilley recalls that as the company compared different products and the vendors representing them, one solution quickly rose to the top: Microsoft Dynamics GP, together with Vicinity Manufacturing, represented by NexTec. “It was a complete solution at the right price,” Reilley says. “NexTec’s expertise was evident during the demonstrations. They asked the right questions and showed us precisely how they could address our requirements.”
Streamline order entry
Order entry had been a slow process. The staff had to manually produce the Material Safety Data Sheets (MSDS), Certificate of Analysis (COA), and Department of Transportation (DOT) required shipping documents for every order. “They were going back and forth between Word, Excel, and Peachtree to complete even the most straightforward order,” recalls Reilley.
NexTec streamlined the entire process by adding a new shortcut to the order entry screen. The button launches a process that dynamically creates all the required documentation based on the actual items and lot numbers referenced on the order. “We have halved the time it takes to produce an order,” says Reilley. “That’s significant because it allowed us to grow without hiring additional customer service staff.”
Focus on quality
Columbia Chemical is ISO 9001 registered. As part of its certification requirement, the company must thoroughly document its manufacturing process and the quality assurance testing it performs. Previously this was a tremendously burdensome job. Several spreadsheets were maintained holding batch information and testing results. Now, the software automatically maintains the detailed records required as a part of daily operations.
The Vicinity Manufacturing software tracks all quality control (QC) results by batch and formula and stores them centrally. As QC results are entered, the software warns the staff if a value outside of the accepted range is entered. This eliminates typos and ensures consistent quality. Columbia Chemical can then query these results over time by batch, formula or test, and share the data with statistical analysis packages for deeper evaluation. COA forms are centrally generated from the QC results and tracked by batch, formula and raw-material lot. They can be viewed and printed for one or more formula batches, for finished goods, or for all lots on a sales order.
Centralize data
The integration between Microsoft Dynamics GP and Vicinity Manufacturing eliminates the need for duplicate data entry between the company’s manufacturing and distribution functions. As batches are completed in Vicinity Manufacturing they are instantly recorded to the Dynamics GP Inventory module. Lot numbers and the COA follow an item throughout the system ensuring all departments have access to the vital production data they need.
Control inventory
Reilley says one of the biggest benefits of the company’s new solution is tighter inventory control. “We weren’t able to accurately manage a perpetual inventory before,” he recalls. “As a result we always had to physically check stock before ordering or before a big production run. It took a lot of time and it was risky to not have better accounting for an expensive asset such as our inventory.”
Now Columbia Chemical has precise cost tracking for every batch it produces. Rather than simply using the standard cost of an item, the software uses the actual cost associated with each item used in production run. “Our financial reports are much more accurate now and the accurate cost information helps us make strategic pricing decisions,” Reilley notes.
Great chemistry
“We give NexTec a lot of credit for the success of this project — the chemistry just worked,” concludes Reilley.“They understood where we were and where we wanted to be—perhaps better than we did.
“It allowed us to grow without hiring additional customer service staff.” Kevin Reilley, VP Operations Columbia Chemical
About NexTec Group
NexTec Group is one of North America’s largest and most experienced technology consulting firms, specializing in industry-specific solutions for mid-sized organizations. For nearly 30 years, NexTec has been a trusted partner to businesses, delivering, implementing and supporting the core Enterprise Resource Planning (ERP) solutions they need to scale and grow. NexTec is a gold-certified Acumatica partner with deep experience in field services, manufacturing, distribution, professional services, and more.