Customer Success Story
Empire Candle Co.
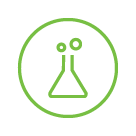
Industry
Process Manufacturing
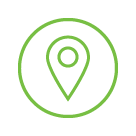
Location
Kansas City, KS
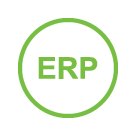
System Selected
Sage X3
Key Results
NexTec helps us continually improve by introducing progressive new ways of getting things done. They are a segment leader – second to none.
Their Story
The United States’ candle industry is worth almost $4 billion annually – and it is still growing. It seems we just can’t get enough of the warm glow, enticing scents and mood-setting capacities of candles. Empire Candle Co., LLC a 67-year veteran of the industry, understands what customers want, and continues to grow both its revenues and market share. The key to the company’s ongoing success is its lean and efficient manufacturing processes which enables it to minimize waste, quickly respond to trends and anticipate customer demand. It’s a process that was honed and perfected through Empire Candle’s partnership with Sage X3 and NexTec Group.
“NexTec helps us continually improve by introducing progressive new ways of getting things done. They are a segment leader – second to none.” Austin Mathis, IT Director, Empire Candle Co., LLC.
“We have grown significantly, both organically and through acquisitions,” explains Austin Mathis, IT Director for Empire Candle. “But our manufacturing practices hadn’t been keeping up with the growth, and were too complex to scale efficiently. We found ourselves over-buying, over-producing and over-extending.”
Illuminating inefficiencies
The company had been using Sage X3 for several years, but the product hadn’t been configured optimally to allow the Empire Candle to leverage its manufacturing capabilities. “We reached a decision point,” recalls Mathis. “Abandon Sage X3, or find someone who could fix our implementation.”
Fortunately for Empire Candle, Mathis found NexTec, one of the premier Sage X3 business partners in the world. “They are a talented, high-caliber group of professionals,” he says. “We brought them in to do a comprehensive review, and then hired them to optimize LLC the implementation. NexTec introduced us to new capabilities and processes that allow us to leverage the software’s capabilities and incorporate best practices. They thoroughly understand Sage X3 and manufacturing. But more importantly, before they offered advice on optimization, they took the time to learn and understand our business, first. The optimization was a great success.”
Firing up operations
The improvements introduced as a result of NexTec’s optimization of Sage X3 have been nothing short of extraordinary. “We’ve significantly reduced our inventory of raw materials and have decreased our production lead times,” says Mathis. “We also have much greater accuracy throughout the supply chain. Before we would often have big discrepancies during physical counts, and now we are spot on.”
The company’s on-time and complete shipment rates have seen dramatic improvement. “Previously we might still be in production when the truck pulled up,” says Mathis. “We’d pay detention fees and incur chargebacks as well as disappoint some customers. Our ability to deliver complete and on-time to our core customer base has improved tremendously.”
Production costs down 30%
Through process improvements including flattening the Bills of Material, work order material picking and staging efficiencies, Empire Candle’s production costs are down by 30 percent, and orders are complete and ready for delivery well ahead of time.
Labor costs are down as well. “Previously we’d run two, sometimes even three shifts during our peak production season, utilizing a heavy temporary staffing population during those fluctuations,” explains Mathis. “Now we have a more stable full-time workforce and operate with a single shift more consistently each year.”
Without reliable planning forecast capabilities, Empire Candle found itself over-buying and over producing, which proved costly. “We’d end up with too much product or too much of the wrong product so we’d end up selling the excess to close out customers,” says Mathis. “Now we have aligned our buying and our production with anticipated demand and can better manage inventory, both raw material and finished goods, at appropriate levels within each of our local facilities.”
$400,000 annual savings
Perhaps the biggest single win for the company was its ability to eliminate an entire overflow warehouse resulting in an annual savings of $400,000. “By honing our manufacturing process, right-sizing our company, reducing waste and focusing on a best-in-class strategy, we were able to reduce our footprint and continue to grow profitably,” says Mathis.
Maintaining high standards
Under NexTec’s advice, Empire Candle began exploring the Quality Control features in Sage X3, and it’s paying off.
“As we pursue new business opportunities, we need to demonstrate our GMP (Good Manufacturing Practices) to potential customers,” Mathis says. “We recently went through a GMP audit and scored an amazing 94 out of 100.”
The company has plans to implement the advanced lot control, traceability and recall management capabilities in Sage X3. While not required, Empire Candle predicts that it will only add to its cadre of best practices and improve its overall efficiency and productivity.
Deep business insight
With NexTec’s expertise and guidance, Empire Candle is leveraging Sage Enterprise Intelligence to gain deep business insight and make strategic, informed decisions regarding its SKU count, to improve real-time performance feedback to functional teams, and to provide sales and marketing teams with self-serve data and analytics.
Glowing endorsement
Mathis has nothing but praise for NexTec. “They engage with us and with our business in a way that’s not typical,” he says. “Their dedication is uncanny. NexTec helps us continually improve by introducing progressive new ways of getting things done. They are a segment leader – second to none.”
He concludes, “Our goal is to continue to grow and improve, and we know we have the product and the partner to help us achieve that goal.”
About NexTec Group
NexTec Group is one of North America’s largest and most experienced technology consulting firms, specializing in industry-specific solutions for mid-sized organizations. For nearly 30 years, NexTec has been a trusted partner to businesses, delivering, implementing and supporting the core Enterprise Resource Planning (ERP) solutions they need to scale and grow. NexTec is a gold-certified Acumatica partner with deep experience in field services, manufacturing, distribution, professional services, and more.